Turn Your Old Laptop Into a DIY Hideaway Media Center for TV
Jan 25, 2016
Turn Your Old Laptop Into a DIY Hideaway Media Center for TV
Turn Your Old Laptop Into a DIY Hideaway Media Center for TV:
Turn Your Old Laptop Into a DIY Hideaway Media Center for TV
Turn Your Old Laptop Into a DIY Hideaway Media Center for TV
Remote Wi-Fi DHT11 Temperature an Humidity I2C 2 X 16 LCD Display With Two ESP8266 and Visuino
Remote Wi-Fi DHT11 Temperature an Humidity I2C 2 X 16 LCD Display With Two ESP8266 and Visuino:
ESP8266 modules are great low cost stand alone controllers with built in Wi-Fi, and I already made a simple Blink instructable with ESP8266 NodeMCU module.The advantage of the ESP8266 over Arduino and other controllers is the builtin Wi-Fi. In this Instructable I will show you how with the help of V...
By: BoianM
Continue Reading »
ESP8266 modules are great low cost stand alone controllers with built in Wi-Fi, and I already made a simple Blink instructable with ESP8266 NodeMCU module.The advantage of the ESP8266 over Arduino and other controllers is the builtin Wi-Fi. In this Instructable I will show you how with the help of V...
By: BoianM
Continue Reading »
Arduino As Stand Alone. Burn Bootloader.
Arduino As Stand Alone. Burn Bootloader.:
Sometimes I need quick hint how to create standalone arduino MC, but when I click buttons in wrong order or connect wires in a wrong way, it brings me to frustration and extra time to figure out where is the problem. So here is quick screenshots of step by step bootloader burn and sketch upload.
By: aequanimitas
Continue Reading »
Sometimes I need quick hint how to create standalone arduino MC, but when I click buttons in wrong order or connect wires in a wrong way, it brings me to frustration and extra time to figure out where is the problem. So here is quick screenshots of step by step bootloader burn and sketch upload.
By: aequanimitas
Continue Reading »
LM35 Temperature Sensor with Datalogging on SD card on Intel Edison
LM35 Temperature Sensor with Datalogging on SD card on Intel Edison:
- Demonstrates the use of an LM35 sensor on Intel Edison to measure temperature over extended periods ranging from several hours to weeks and logs the temperature readings from the sensor to an SD card inserted onboard, all necessary things such as time interval between two consecutive readings, eit...
By: vishal1502
Continue Reading »
- Demonstrates the use of an LM35 sensor on Intel Edison to measure temperature over extended periods ranging from several hours to weeks and logs the temperature readings from the sensor to an SD card inserted onboard, all necessary things such as time interval between two consecutive readings, eit...
By: vishal1502
Continue Reading »
Ir Remote Camera Shutter for Android Phone
Ir Remote Camera Shutter for Android Phone:
For you're like photo selfie, definitely should have a tool that could make it easier to take foto.there are some tools that can be used which can be purchased at amazon(or other online shop).you can choose between taking the cable connected headset or connected with bluetooth.now i make which can b...
By: agoe3es_one
Continue Reading »
For you're like photo selfie, definitely should have a tool that could make it easier to take foto.there are some tools that can be used which can be purchased at amazon(or other online shop).you can choose between taking the cable connected headset or connected with bluetooth.now i make which can b...
By: agoe3es_one
Continue Reading »
2 MINUTE ARDUINO LASER ALARM
2 MINUTE ARDUINO LASER ALARM:
WHAT YOU NEEDArduino LaserBreadboardJumper wiresLED10K Resistor CONNECTIONS First connect you resistor to the photo resistor and then that end will go to the - row in the board then the photo resistor will go to A0 on the arduino and the other end to 5V and the LED simply goes to pin 13 on the a...
By: Jacks how2s
Continue Reading »
WHAT YOU NEEDArduino LaserBreadboardJumper wiresLED10K Resistor CONNECTIONS First connect you resistor to the photo resistor and then that end will go to the - row in the board then the photo resistor will go to A0 on the arduino and the other end to 5V and the LED simply goes to pin 13 on the a...
By: Jacks how2s
Continue Reading »
Burning an Arduino bootloader to a new ATMEGA328-AU chip #Arduino
Burning an Arduino bootloader to a new ATMEGA328-AU chip #Arduino:
Thanks to Lalindra for sending in this video! Lalindra writes:
Thanks to Lalindra for sending in this video! Lalindra writes:
Just wanted to share a video that I created. Its on how to burn an Arduino bootloader to a new ATMEGA328-AU chip.See more
Jan 24, 2016
Make a workbench fan from an old microwave oven exhaust fan
Make a workbench fan from an old microwave oven exhaust fan:
I always like to salvage usable parts off of things before I recycle them. So when replacing a microwave oven, I salvaged the fan and starter capacitor.I found this two-speed fan to be quite-powerful (300-400 cfm), and directional. Which gave me the idea of making a fan for my workbench that blew ac...
By: psdhowto
Continue Reading »
I always like to salvage usable parts off of things before I recycle them. So when replacing a microwave oven, I salvaged the fan and starter capacitor.I found this two-speed fan to be quite-powerful (300-400 cfm), and directional. Which gave me the idea of making a fan for my workbench that blew ac...
By: psdhowto
Continue Reading »
How to Build a Wankel Engine (and How It Works)
How to Build a Wankel Engine (and How It Works):
This is for my AP Physics C class.Wankel Rotary engines are quite ingenious. They arose as an attempt to challenge piston-based engines, and proved that sufficient power can be created without the reciprocating motion of pistons. They rely on very few moving parts to produce a power output and manag...
By: stoyanAPC
Continue Reading »
This is for my AP Physics C class.Wankel Rotary engines are quite ingenious. They arose as an attempt to challenge piston-based engines, and proved that sufficient power can be created without the reciprocating motion of pistons. They rely on very few moving parts to produce a power output and manag...
By: stoyanAPC
Continue Reading »
Simple small QRO for HF
Simple small QRO for HF:

Marko Pavlin has been working on a HF amplifier project:
Marko Pavlin has been working on a HF amplifier project:
I followed the ARRL Homberw challenge 50 watt aplifier entry. It is low cost, simple HF linear amplifier designed and built by the author as an entry in the ARRL’s 2009 Homebrew Challenge contest. The requirements of the amplifier were: 40 meter band 50 watt output amplifier intended for use with a QRP transmitter as driver (less than 5W), constructed at a total material cost of not over $125.00.Project info at Mare & Gal Electronics homepage.
I redesigned author original design an put it on the double sided PCB with additional output banpass filters. I started with first prototype. It worked quite well for short periods. Main disadvantage was lack of heat sink. Then I soldered second prototype with proper transistor cooling. I also wound correct transformer using binocular ferrite cores
Next step was designing PCB. I started with the schematic diagram based on original project
ESP8266 mains energy monitor
ESP8266 mains energy monitor:
Brian Dorey has designed a mains energy monitor based on ESP8266 that have sensors for the mains current, electric meter and gas meter.
The post ESP8266 mains energy monitor appeared first on Electronics-Lab.
Brian Dorey has designed a mains energy monitor based on ESP8266 that have sensors for the mains current, electric meter and gas meter.
As the new solar logger did not have this functionality we decided to design a new data-logger that would measure not only the mains current usage but also keep track of the electric meter and gas meter so we can easily see how much energy we are using in the house.ESP8266 mains energy monitor – [Link]
The new mains energy monitor was designed to be a standalone box that would be powered from the mains and have sensors for the mains current, electric meter and gas meter. As we didn’t want to run any more wires around the house we also decided to make it wireless connecting to our network over Wi-Fi.
The post ESP8266 mains energy monitor appeared first on Electronics-Lab.
Battery Powered Frequency Meter (0 to 20kHz)
Battery Powered Frequency Meter (0 to 20kHz):
The circuit is a simple digital frequency meter that is made of a frequency-to-voltage converter and an analog-to-digital display converter that can be operatedfrom a single 9-volt battery. The TC7126 ADC generates the voltage required by the TC9400 FVC with internal regulators. The TC7126 is designed to directly drive a 3-1/2 digit, non-multiplexed LCD display so no digital conversion is required.
The input circuit is made up of a current limiting resistor (33kΩ), a DC blocking capacitor (0.01µF), a clamping diode (1N914), and a biasing resistor (1MΩ). The diode acts as a soft clamp to prevent negative going transitions from latching the comparator input and the 33kΩ resistor limits the current during the positive transitions. The gain (VOUT vs. FREQIN) of the TC9400 is determined by the charge-balance capacitor and the integrator feedback resistor (620kΩ) that has been selected for an output of approximately +2V (referenced to ANALOG COMMON) with frequency input of 20kHz. The bias resistor (12kΩ) determined the input threshold of the comparator and has been selected for an input sensitivity range of 250mV to 10V peak-to-peak of a sine or square wave on the input of the FVC.
The TC7126 will have a maximum positive input of about 2V since the input is referenced to ANALOG COMMON that is only 3V below V+. The internal voltage swing of the integrator does not have the same limitation because a positive input results in a negative swing of the integration. A fully charged battery will give a range of about 6V. The integration components (1MΩ and 0.047µF) at pins VBUFF and VIN are selected, in conjunction with the oscillator frequency to have an integrator ramp amplitude of about –3V with a 2V input from the TC9400. The oscillator is set up to run at 48kHz (150kΩ and 50pF) for maximum rejection of stray power-line pickup. This will result in the TC7126 running at three conversions per second.
Battery Powered Frequency Meter (0 to 20kHz) – [Link]
The post Battery Powered Frequency Meter (0 to 20kHz) appeared first on Electronics-Lab.
The circuit is a simple digital frequency meter that is made of a frequency-to-voltage converter and an analog-to-digital display converter that can be operatedfrom a single 9-volt battery. The TC7126 ADC generates the voltage required by the TC9400 FVC with internal regulators. The TC7126 is designed to directly drive a 3-1/2 digit, non-multiplexed LCD display so no digital conversion is required.
The input circuit is made up of a current limiting resistor (33kΩ), a DC blocking capacitor (0.01µF), a clamping diode (1N914), and a biasing resistor (1MΩ). The diode acts as a soft clamp to prevent negative going transitions from latching the comparator input and the 33kΩ resistor limits the current during the positive transitions. The gain (VOUT vs. FREQIN) of the TC9400 is determined by the charge-balance capacitor and the integrator feedback resistor (620kΩ) that has been selected for an output of approximately +2V (referenced to ANALOG COMMON) with frequency input of 20kHz. The bias resistor (12kΩ) determined the input threshold of the comparator and has been selected for an input sensitivity range of 250mV to 10V peak-to-peak of a sine or square wave on the input of the FVC.
The TC7126 will have a maximum positive input of about 2V since the input is referenced to ANALOG COMMON that is only 3V below V+. The internal voltage swing of the integrator does not have the same limitation because a positive input results in a negative swing of the integration. A fully charged battery will give a range of about 6V. The integration components (1MΩ and 0.047µF) at pins VBUFF and VIN are selected, in conjunction with the oscillator frequency to have an integrator ramp amplitude of about –3V with a 2V input from the TC9400. The oscillator is set up to run at 48kHz (150kΩ and 50pF) for maximum rejection of stray power-line pickup. This will result in the TC7126 running at three conversions per second.
Battery Powered Frequency Meter (0 to 20kHz) – [Link]
The post Battery Powered Frequency Meter (0 to 20kHz) appeared first on Electronics-Lab.
555 Based DC Motor Speed Controller
555 Based DC Motor Speed Controller:
555 DC Motor Speed Controller project will control the speed of a DC motor connected to it. This project is built using the popular 555 timer IC.
Specifications
The post 555 Based DC Motor Speed Controller appeared first on Electronics-Lab.
555 DC Motor Speed Controller project will control the speed of a DC motor connected to it. This project is built using the popular 555 timer IC.
Specifications
- Power supply input 5-12V DC
- Motor Load Up to 1 to 2Amps
- Onboard preset to vary Duty Cycle from 10% to 95% @ 120 Hz
- Ideal for mini drill and robotics application
- Transistor based output drive with heat-sink
- Diode protection for motor surge
- Power-On LED indicator
- Screw terminal connector for easy power supply input and output-Motor connection
- Four mounting holes of 3.2 mm each
- PCB dimensions 47 mm x 56 mm
The post 555 Based DC Motor Speed Controller appeared first on Electronics-Lab.
Simple Arduino SD-Card GPS/NMEA Datalogger
Simple Arduino SD-Card GPS/NMEA Datalogger:
KF5OBS @ jaunty-electronics.com shows us how to build a minimalistic GPS datalogger. The GPS logger is based on the Arduino platform and stores raw NMEA sentences from pretty much any GPS module to a SD card.
The post Simple Arduino SD-Card GPS/NMEA Datalogger appeared first on Electronics-Lab.
KF5OBS @ jaunty-electronics.com shows us how to build a minimalistic GPS datalogger. The GPS logger is based on the Arduino platform and stores raw NMEA sentences from pretty much any GPS module to a SD card.
For a project I needed to log GPS information. I had various GPS modules and plenty of Arduinos laying around the lab. At first I intended for the Arduino to capture data from the GPS module, process it and then store it onto a SD card. However, I discarded that idea in favor of more flexibility and now use the arduino merely as pass-thru device for the raw GPS data.Simple Arduino SD-Card GPS/NMEA Datalogger – [Link]
The post Simple Arduino SD-Card GPS/NMEA Datalogger appeared first on Electronics-Lab.
Up Your Tiny House Game with Stone Age Hacks
Up Your Tiny House Game with Stone Age Hacks:
Bare feet, bare hands, and bare chest – if it weren’t for the cargo shorts and the brief sound of a plane overhead, we’d swear the video below was footage that slipped through a time warp. No Arduinos, no CNC or 3D anything, but if you doubt that our Stone Age ancestors were hackers, watch what [PrimitiveTechnology] goes through while building a tile-roofed hut with no modern tools.
The first thing we’ll point out is that [PrimitiveTechnology] is not attempting to be (pre-)historically accurate. He borrows technology from different epochs in human history for his build – tiled roofs didn’t show up until about 5,000 years ago, by which time his stone celt axe would have been obsolete. But the point of the primitive technology hobby is to build something without using any modern technology. If you need a fire, you use a fire bow; if you need an axe, shape a rock. And his 102 day build log details every step of the way. It’s fascinating to watch logs, mud, saplings, rocks and clay come together into a surprisingly cozy structure. Especially awesome if a bit anachronistic is the underfloor central heating system, which could turn the hut into a lovely sauna.
Primitive technology looks like a fascinating hobby with a lot to teach us about how we got to now. But if you’re not into grubbing in the mud, you could always 3D print a clay hut. We’re not sure building an enormous delta-bot is any easier, though.
https://www.youtube.com/watch?v=P73REgj-3UE
Thanks to [Rockyd] for the tip.
Bare feet, bare hands, and bare chest – if it weren’t for the cargo shorts and the brief sound of a plane overhead, we’d swear the video below was footage that slipped through a time warp. No Arduinos, no CNC or 3D anything, but if you doubt that our Stone Age ancestors were hackers, watch what [PrimitiveTechnology] goes through while building a tile-roofed hut with no modern tools.
The first thing we’ll point out is that [PrimitiveTechnology] is not attempting to be (pre-)historically accurate. He borrows technology from different epochs in human history for his build – tiled roofs didn’t show up until about 5,000 years ago, by which time his stone celt axe would have been obsolete. But the point of the primitive technology hobby is to build something without using any modern technology. If you need a fire, you use a fire bow; if you need an axe, shape a rock. And his 102 day build log details every step of the way. It’s fascinating to watch logs, mud, saplings, rocks and clay come together into a surprisingly cozy structure. Especially awesome if a bit anachronistic is the underfloor central heating system, which could turn the hut into a lovely sauna.
Primitive technology looks like a fascinating hobby with a lot to teach us about how we got to now. But if you’re not into grubbing in the mud, you could always 3D print a clay hut. We’re not sure building an enormous delta-bot is any easier, though.
https://www.youtube.com/watch?v=P73REgj-3UE
Thanks to [Rockyd] for the tip.
How to Use Lidar with the Raspberry Pi
How to Use Lidar with the Raspberry Pi:
The ability to inexpensively but accurately measure distance between an autonomous vehicle or robot and nearby objects is a challenging problem for hackers. Knowing the distance is key to obstacle avoidance. Running into something with a small robot may be a trivial problem but could be deadly with a big one like an autonomous vehicle.
My interest in distance measurement for obstacle avoidance stems from my entry in the 2013 NASA Sample Return Robot (SRR) Competition. I used a web camera for vision processing and attempted various visual techniques for making measurements, without a lot of success. At the competition, two entrants used scanning lidars which piqued my interest in them.
A lidar is a laser range measurement device. The name is a combination of the terms LIght and raDAR and not, as commonly suggested, an acronym derived in a manner similar to its forerunner, “RAdio Detection And Ranging”. The term was first used in 1963 according to Merriam-Webster. Some of the early use of lidar was measuring clouds and the surface of the moon by Apollo 13. As lasers were reduced in size, other uses were found, including as a rangefinder for military purposes.

A single laser beam can only provide the range to a single object. Just as aircraft control radar swings a beam through the sky, a scanning lidar sweeps the laser. The application of lidar for autonomous mobile devices requires scanning of a wide area both vertically and horizontally to provide a point cloud of distance measurements. Something similar might be done with an infra-red sensor, as we’ve seen previously but the accuracy is not as good as with a laser.
Distance measurement can be done in multiple ways but there are two principal ones used. One measures the time of flight of a laser pulse while the other uses the angle of deflection of the laser beam.
As you might suspect things get tricky given the speed of light. A pioneer in computers, Rear Admiral Grace “Amazing Grace” Hopper would hand out 11.80” pieces of wire to demonstrate the distance light travels in a nanosecond in vacuum. With robots that is the magnitude of the distance we’re interested in measuring. It’s difficult to measure less than a meter sending out just a pulse and timing the return signal because the signal returns in about 7 nanoseconds.
One technique around this is to continuously modulate the signal by amplitude or frequency. The phase difference between the transmitted and received signals is proportional to the distance to the object. A lidar using modulation can measure down to centimeters.
There are a number of commercial providers of ToF based scanning lidars but the price is a bit higher than the most hobbyist’s would spend. A relatively new entrant, PulsedLight, offered a single beam ToF lidar within the price range of hackers but their suppliers are all back ordered.

The Optical Society describes these and other techniques used for measuring distance.
Sparkfun did a tear down of the vacuum and investigated the lidar. A long discussion starting in November of 2010 ensued on the Trossen Robotic forum as hackers dissected the vacuum with much attention to the lidar. There were even small prizes offered for hacking the lidar.
Unfortunately a number of the links in that thread no longer exist but it is still worth reading since many details are laid out in the messages. Some other threads on the forum have additional information. One especially interesting find is a research paper that preceded the Neato lidar but served as the basis for the final design. It outlined the details necessary for Neato to create an engineered product.
The good news is a wiki exists with a summary of information about the vacuum and the lidar. One of the active hacking participants, [Nicolas “Xevel” Saugnier] created a small USB interface board to power the lidar and connect to its serial interface. In the summer of 2014 I obtained a couple of the lidar units and the boards as I looked toward entering the 2015 NASA SRR. I got the lidar units working using [Xevel’s] Python software and packages available in the Robot Operating System.
The scanning lidar allowed Neato Robotics to implement Simultaneous Localization and Mapping (SLAM) using the distance measurement data. This allows the robot to plan the cleaning path rather than using the previous bump and random movements, a Drunkard’s Walk, of earlier vacuums. This allows the Neato to completely cover a room more quickly. Note in this video of a Neato demonstration how the robot builds a map of where it’s been and the obstacles it encounters. Especially note how it uses the lidar data to neatly circle the one obstacle.
In the vacuum, the motor is powered by a 12V source using PWM at around a 25% duty cycle. This means the motor needs around 3V to run at the right speed and subsequent testing by the hackers showed this is true. The USB interface board runs the lidar from the 5V input from the USB connector using PWM controlled by a a PID (Proportional Integral Differential) loop to maintain the motor’s speed. Why use PWM and PID? To maintain a constant RPM for the spinning turret as it wears and collects dirt, dust, and other detritus. In my testing I noted that the motor will turn the turret in either direction depending on the positive and negative connection. The interface still works fine but the sequence of the data points is going to be reversed. Normally the turret turns counter-clockwise.
A word of caution: in some early units the interface used 3V3 so connecting them to 5V may destroy the interface.
My original hook-up between the Pi and the lidar was quick and dirty. I connected the motor to the Pi’s 3V3 output and it worked. The output from the Pi 3V3 is limited to 50 mA by the specifications and the lidar Wiki says the motor would draw 64 mA. I measured mine and it drew considerably more. I also connected the interface’s TX pin to the Pi’s RX (pin 10). Using CuteCom under Raspbian Jessie I could read the data when the turret was manually spun. With those basic tests out of the way it was time to get a little more serious.
I elected to use a ULN2803A Darlington Transistor Array I found in my parts cabinet to drive the motor. This IC easily handles the current needed to drive the motor and includes the protective diodes required for driving an inductive load. I didn’t intended to do PWM of the motor but did want to turn it off and on. I connected the Pi’s 5V on pin 2 to the red wire on the motor connector. The black wired connected to the ULN2803A through a 15 ohm resistor to drop the voltage. This setup low-side configuration for controlling the motor. The interface cable is connected to the 5V, ground, and RX pins on the Pi.

To test the motor control I used the mapping of the GPIO pins to the file system directory /sys/class/gpio. Each GPIO can be controlled here once the pin is exported. Commands can then set pins the direction and turn the pin on and off. The commands I used controlled GPIO 18 (pin 12):
One interesting result occurs if you are connected to the serial port and then apply power to the interface. The lidar generates a welcome message:
While looking for information on programming the GPIO with C++ I found the WiringPi library by [Gordon Henderson]. It not only supports raw GPIO programming but supports many Pi daughter boards. An additional appeal to me is it has a serial port interface so I didn’t have to get into the details of that on Linux, which would have been new to me. Eventually, I even used its simple thread capability to handle an absurdly minimal user interface. [Gordon] also has a utility you should check out for controlling pins from the command line more completely than writing to the directories as I showed above.
The final piece I found in WiringPi is the ability to do hardware PWM on the one GPIO pin capable of it on the Pi. That is GPIO 18. I’d originally used GPIO 4 (pin 7) to control the motor but switched when I found this capability. The code currently sets a constant value for the PWM but eventually I want to add (and write an article about) a PID (Proportional Integral Differential) control system loop to maintain constant speed. Setting up WiringPi, a thread and the the PWM on GPIO 18 is easy:
Next steps are to get the checksum routine working, expand the so-called user interface to allow controlling operation of the turret and adding a PID loop to maintain a constant speed of rotation. Since the UNL2803A chip is there I’ll use it to control the power to the interface. I also want to look at cross-compiling the code from my desktop and doing remote debugging. As I make those changes I’ll organize the code into classes and see how I can use it on a robot.
Filed under: Hackaday Columns, how-to, Raspberry Pi, robots hacks

The ability to inexpensively but accurately measure distance between an autonomous vehicle or robot and nearby objects is a challenging problem for hackers. Knowing the distance is key to obstacle avoidance. Running into something with a small robot may be a trivial problem but could be deadly with a big one like an autonomous vehicle.
My interest in distance measurement for obstacle avoidance stems from my entry in the 2013 NASA Sample Return Robot (SRR) Competition. I used a web camera for vision processing and attempted various visual techniques for making measurements, without a lot of success. At the competition, two entrants used scanning lidars which piqued my interest in them.
A lidar is a laser range measurement device. The name is a combination of the terms LIght and raDAR and not, as commonly suggested, an acronym derived in a manner similar to its forerunner, “RAdio Detection And Ranging”. The term was first used in 1963 according to Merriam-Webster. Some of the early use of lidar was measuring clouds and the surface of the moon by Apollo 13. As lasers were reduced in size, other uses were found, including as a rangefinder for military purposes.

A single laser beam can only provide the range to a single object. Just as aircraft control radar swings a beam through the sky, a scanning lidar sweeps the laser. The application of lidar for autonomous mobile devices requires scanning of a wide area both vertically and horizontally to provide a point cloud of distance measurements. Something similar might be done with an infra-red sensor, as we’ve seen previously but the accuracy is not as good as with a laser.
Distance measurement can be done in multiple ways but there are two principal ones used. One measures the time of flight of a laser pulse while the other uses the angle of deflection of the laser beam.
Time of Flight Measurement
You’re familiar with how basic radar and sonar works – send out a pulse and measure the time it takes to receive the return signal. The time divided by the speed of light or sound gives you the distance the signal traveled out and back. Divide that by two to get the distance to the object. That’s time of flight (ToF) measurement.As you might suspect things get tricky given the speed of light. A pioneer in computers, Rear Admiral Grace “Amazing Grace” Hopper would hand out 11.80” pieces of wire to demonstrate the distance light travels in a nanosecond in vacuum. With robots that is the magnitude of the distance we’re interested in measuring. It’s difficult to measure less than a meter sending out just a pulse and timing the return signal because the signal returns in about 7 nanoseconds.
One technique around this is to continuously modulate the signal by amplitude or frequency. The phase difference between the transmitted and received signals is proportional to the distance to the object. A lidar using modulation can measure down to centimeters.
There are a number of commercial providers of ToF based scanning lidars but the price is a bit higher than the most hobbyist’s would spend. A relatively new entrant, PulsedLight, offered a single beam ToF lidar within the price range of hackers but their suppliers are all back ordered.

Triangulation
The triangulation lidar uses the same technique as the Sharp infra-red distance measuring sensors which hackers have been using for years. The transmitter is a single source but the receiver is a 1 or 2 dimensional array of receivers. The offset of the receiver elements from the transmitter creates the baseline of a triangle. The outgoing and return signal are the other two sides of the triangle. Simple trigonometry provides the distance from the baseline to the object.The Optical Society describes these and other techniques used for measuring distance.
Neato Robotics Vacuum Lidar
What I didn’t know when competing in the 2013 NASA SRR is that Neato Robotics released a vacuum cleaner in 2010 using a scanning lidar to sense the vacuum’s surroundings. This allows the robot to avoid obstacles instead of bumping into them as previous robot vacuum’s were doing.
Unfortunately a number of the links in that thread no longer exist but it is still worth reading since many details are laid out in the messages. Some other threads on the forum have additional information. One especially interesting find is a research paper that preceded the Neato lidar but served as the basis for the final design. It outlined the details necessary for Neato to create an engineered product.
The good news is a wiki exists with a summary of information about the vacuum and the lidar. One of the active hacking participants, [Nicolas “Xevel” Saugnier] created a small USB interface board to power the lidar and connect to its serial interface. In the summer of 2014 I obtained a couple of the lidar units and the boards as I looked toward entering the 2015 NASA SRR. I got the lidar units working using [Xevel’s] Python software and packages available in the Robot Operating System.
The scanning lidar allowed Neato Robotics to implement Simultaneous Localization and Mapping (SLAM) using the distance measurement data. This allows the robot to plan the cleaning path rather than using the previous bump and random movements, a Drunkard’s Walk, of earlier vacuums. This allows the Neato to completely cover a room more quickly. Note in this video of a Neato demonstration how the robot builds a map of where it’s been and the obstacles it encounters. Especially note how it uses the lidar data to neatly circle the one obstacle.
Pi 2 and Lidar
I’m still very interested in robots although I’ve given up on the SRR contest. The lidars have been sitting on the shelf luring me like mythical Sirens. I finally succumbed to their call when I realized the lidar serial interface was a perfect match to a Raspberry Pi’s since both work at 3V3 levels. This would eliminate the USB interface. A similar effort is [Thomas Jesperson’s] in 2014 who used an STM32F429 board and produced a video of the lidar in action.Lidar Physical
The lidar is a sealed unit with a motor hanging from one end. The motor drives a turret that rotates at around 300 rpm. The turret contains the laser and receive sensor and by spinning provides a 360 degree scan of the surrounding area. The laser and receive sensor have two optical ports out of the turret. There are two short cables with JST connectors coming from the lidar. A two pin connector provides power to the motor. A four pin connector provides 5V power to the control circuits and the 3V3 serial interface. The pinouts are:Motor Cable
Red: 3V3 or PWM
Black: Ground
Red: 3V3 or PWM
Black: Ground
Interface Cable
Black: Ground
Red: 5V
Brown: RX
Orange: TX
Black: Ground
Red: 5V
Brown: RX
Orange: TX
A word of caution: in some early units the interface used 3V3 so connecting them to 5V may destroy the interface.
My original hook-up between the Pi and the lidar was quick and dirty. I connected the motor to the Pi’s 3V3 output and it worked. The output from the Pi 3V3 is limited to 50 mA by the specifications and the lidar Wiki says the motor would draw 64 mA. I measured mine and it drew considerably more. I also connected the interface’s TX pin to the Pi’s RX (pin 10). Using CuteCom under Raspbian Jessie I could read the data when the turret was manually spun. With those basic tests out of the way it was time to get a little more serious.
I elected to use a ULN2803A Darlington Transistor Array I found in my parts cabinet to drive the motor. This IC easily handles the current needed to drive the motor and includes the protective diodes required for driving an inductive load. I didn’t intended to do PWM of the motor but did want to turn it off and on. I connected the Pi’s 5V on pin 2 to the red wire on the motor connector. The black wired connected to the ULN2803A through a 15 ohm resistor to drop the voltage. This setup low-side configuration for controlling the motor. The interface cable is connected to the 5V, ground, and RX pins on the Pi.

To test the motor control I used the mapping of the GPIO pins to the file system directory /sys/class/gpio. Each GPIO can be controlled here once the pin is exported. Commands can then set pins the direction and turn the pin on and off. The commands I used controlled GPIO 18 (pin 12):
echo 18 > /sys/class/gpio/export echo out > /sys/class/gpio/gpio18/direction echo 0 > /sys/class/gpio/gpio18/value echo 1 > /sys/class/gpio/gpio18/valueThe ‘0’ and ‘1’ when echoed turn the pin off and on, respectively. This worked and I could see the data using CuteCom.
One interesting result occurs if you are connected to the serial port and then apply power to the interface. The lidar generates a welcome message:
Piccolo Laser Distance ScannerAlso, if you manually spin the turret, a message saying “Spin” appears and advises there is a command capability available by sending a break or three esc characters. Information on the commands is available on the Wiki.
Copyright (c) 2009-2011 Neato Robotics, Inc.
All Rights Reserved
Loader\0x09V2.5.15295
CPU\0x09F2802x/c001
Serial\0x09KSH34313AA-0140854
LastCal\0x09[5371726C]
Runtime\0x09V2.6.15295
Lidar Software
Now to create some rough software to see how all this works. Of course I used C++ so I installed the tool chain for the Pi 2 and find that the compilation speed is sufficient for development. I started using the Geany programming editor and makefiles; a setup I learned about while working with the Python code for the lidar. It handles multiple programming languages and I’ve adopted it as a general purpose text editor on Ubuntu and Raspian. But I eventually abandoned Geany and installed Eclipse CDT on the Pi when it wouldn’t properly reformat the C++ code after editing. Eclipse works surprisingly well on the Pi. I was actually a little disappointed in the switch since with Geany I was re-learning how to work with makefiles, a skill I’ve lost working with Eclipse.While looking for information on programming the GPIO with C++ I found the WiringPi library by [Gordon Henderson]. It not only supports raw GPIO programming but supports many Pi daughter boards. An additional appeal to me is it has a serial port interface so I didn’t have to get into the details of that on Linux, which would have been new to me. Eventually, I even used its simple thread capability to handle an absurdly minimal user interface. [Gordon] also has a utility you should check out for controlling pins from the command line more completely than writing to the directories as I showed above.
The final piece I found in WiringPi is the ability to do hardware PWM on the one GPIO pin capable of it on the Pi. That is GPIO 18. I’d originally used GPIO 4 (pin 7) to control the motor but switched when I found this capability. The code currently sets a constant value for the PWM but eventually I want to add (and write an article about) a PID (Proportional Integral Differential) control system loop to maintain constant speed. Setting up WiringPi, a thread and the the PWM on GPIO 18 is easy:
wiringPiSetup(); piHiPri(10); // set program priority to run better piThreadCreate(key_read); pinMode(turret, PWM_OUTPUT); pwmWrite(turret, 950);The thread is there simply to stop the program when any key is entered and return hit. When
run
is set to false, the main thread reading the serial input quits and the program exits after turning off the turret. The actual thread is dirt simple:PI_THREAD(key_read) { cin.get(); run = false; return 0; }Reading the serial input is simple, just reading characters, but the data itself, while straightforward, requires a little bit banging. There are 360 samples per revolution of the turret so the amount of data at 5 revolutions per second is massive. There are 90 packets each containing four data points. Each point is represented by four bytes of data: distance, signal strength, invalid distance bit, and invalid strength bit. In addition, each packet begins with a start byte, an index byte which is the packet number, and two bytes for the turret rotation speed. The packet ends with two checksum bytes. Here’s how I mapped that data into structures:
struct DataPoint { bool invalid_data; bool bad_strength; float distance; unsigned int strength; }; struct Block { unsigned int index; unsigned int speed; };I didn’t get into storing the data packets, just reporting them to verify I was seeing good data and my calculations looked good. The distance data is an integer reported in millimeters which I converted to inches. The code for the checksum is on the Wiki but I haven’t implemented it yet.
Wrap Up
This is just the start of working with the Neato lidar but a good one. The hardware works well and the basics of the software are in hand. I can get the data and see that it is valid. The WiringPi library is a good find for continuing in my efforts with the Pi.Next steps are to get the checksum routine working, expand the so-called user interface to allow controlling operation of the turret and adding a PID loop to maintain a constant speed of rotation. Since the UNL2803A chip is there I’ll use it to control the power to the interface. I also want to look at cross-compiling the code from my desktop and doing remote debugging. As I make those changes I’ll organize the code into classes and see how I can use it on a robot.
Filed under: Hackaday Columns, how-to, Raspberry Pi, robots hacks

Jan 19, 2016
Visuino – visual programming environment for Arduino
Visuino – visual programming environment for Arduino:
Visuino is the latest software developed by Mitov Software which allows you to program your Arduino boards using a graphical interface. So far only the official boards are supported but more will come. Using Visuino you can easily create complex programs using drag and drop interface without the need to become expert in programming. Check it out on the link below.
Visuino – visual programming environment for Arduino – [Link]
The post Visuino – visual programming environment for Arduino appeared first on Electronics-Lab.
Visuino is the latest software developed by Mitov Software which allows you to program your Arduino boards using a graphical interface. So far only the official boards are supported but more will come. Using Visuino you can easily create complex programs using drag and drop interface without the need to become expert in programming. Check it out on the link below.
Visuino – visual programming environment for Arduino – [Link]
The post Visuino – visual programming environment for Arduino appeared first on Electronics-Lab.
An ARDUINO based JPEG Camera with IR and PIR | Open Electronics
An ARDUINO based JPEG Camera with IR and PIR | Open Electronics:
An ARDUINO based JPEG Camera with IR and PIR
By Boris Landoni on November 26, 2015
Let’s equip Arduino with a serial-interface JPEG Camera with IR and try two applications: the first one saves shots (on a SD-card) at regular intervals while the second uses a PIR sensor to detect intrusions and photograph what happens.
An ARDUINO based JPEG Camera with IR and PIR
By Boris Landoni on November 26, 2015
Let’s equip Arduino with a serial-interface JPEG Camera with IR and try two applications: the first one saves shots (on a SD-card) at regular intervals while the second uses a PIR sensor to detect intrusions and photograph what happens.
Flyport – Professional IoT modules by OpenPicus
Flyport – Professional IoT modules by OpenPicus:

OpenPicus FlyPort is a system on a module dedicated to IoT and M2M application, especially for professional use. Following some details on the solution:
Source: OpenPicus Flyport – Professional IoT modules
OpenPicus FlyPort is a system on a module dedicated to IoT and M2M application, especially for professional use. Following some details on the solution:
Here is the Flyport Wiki with all the details to use it in a few!Why FlyportPRO SoM?A system-on-module is the best solution for those customers looking for flexibility and for development time and risk reduction. FlyportPRO is already installed in tens of thousands of professional devices around the world and you can rely on our professional support during development.How to create your next IoT/M2M product?Easy, just designing a simple carrier board for it you get three different products. The carrier board is normally very easy to design since you don’t need an host processor there: FlyportPRO acts as core processor and connectivity, all in one. If you want to see how much you save with FlyportPRO instead of design from scratch we made this guide for you.
Embedded development made easyWe provide you a powerful IDE, for free. The IDE manages our powerful real-time framework that manages the connectivity stack and your application, with zero risk and max flexibility for you. You don’t need to struggle with registers and low-level programming: our APIs are there.
Connectivity features
- Web server, HTTP server (only on Wi-Fi/GPRS versions)
- HTTP Client
- FTP Client SMTP, SNTP
- FOTA firmware upgrade over the air (only on Wi-Fi/GPRS versions)
- SSL/TLS security
FlyportPRO pinout
60 pins are available for your application. Most of them are remappable, this means you can adapt the pinout of our module by software.
- Microchip PIC24GB256 processor 16Mbit Flash memory (for FOTA and web pages)
- 30 GPIOs
- 10 Analog inputs (with onboard 2.048V precise voltage reference)
- 4 UART
- 10 PWM
- SPI
- 2 I2C
- Serial bootloader on each module to flash the firmware by UART
Source: OpenPicus Flyport – Professional IoT modules
PXFmini Low Cost Open Autopilot for your RaspberryPi UAV and Drones
PXFmini Low Cost Open Autopilot for your RaspberryPi UAV and Drones:


The PXFmini is a low cost and open autopilot shield for the Raspberry Pi that allows you to create a ready-to-fly autopilot with support for Dronecode’s APM flight stack.
The shield has been designed specially for the Raspberry Pi Zero but it is also compatible with the following boards:
The PXFmini is a low cost and open autopilot shield for the Raspberry Pi that allows you to create a ready-to-fly autopilot with support for Dronecode’s APM flight stack.
The shield has been designed specially for the Raspberry Pi Zero but it is also compatible with the following boards:
- Raspberry Pi
- Raspberry Pi 2
- Raspberry Pi Zero
- BananaPi
- Orange Pi
- Odroid-C1
- Odroid-C1+
- 3 axes gravity sensor
- 3 axes gyroscope
- 3 axes digital compass
- Pressure sensor
- Temperature sensor
- ADC for battery sensing
Today, Erle Robotics announced the launch of the PXF mini. With the small price of $75, the autopilot offers a shield designed for the $5 Raspberry Pi Zero, although it is compatible with the whole Raspberry family. This breakthrough in cost, weight (15g) and size (71x31mm) brings intelligent Linux autopilots to a larger audience of UAV and robot enthusiasts than ever before.Source: PXFmini | Erle Robotics
PXF Mini packs Gravity, Gyroscope, Compass, Pressure, Temperature and Battery Sensors. Its Dronecode connectors make set-up easier and stronger; simply attach to the Raspberry Pi, plug in drone components and you are Ready-To-Fly.
In keeping with Erle’s philosophy, the PXFmini is Open Code so enthusiasts can hack around and create tailored robots from this platform.
PXFmini ships in February and is now available to pre-order
Jan 18, 2016
[DIY] High Current Micro USB Charging Cable From Cheap China Cable
[DIY] High Current Micro USB Charging Cable From Cheap China Cable:
WHY
I use Waze on my N5 every day during my commute to and from work. I find that the only micro USB cable I have that can still charge my N5 while running Waze is the OEM LG cable that came with it. I don't like the current state of affairs - where I'm reliant on just one cable with no backups.
WHAT
I've tried the regular 'Genuine' micro USB cables from China via Ebay that purport to handle Galaxy Note level charging, as well as 24/28 AWG cables that are supposed to handle increased currents. No joy.
NEED
- Pocket Knife
- Soldering iron + associated materials
- Electrical tape
HOW
I used a cheap, China, Ebay, micro USB cable that has a hard plastic casing around the connectors on either end of the cable; this makes it easier to pop the casing off, fiddle with the wires, and close everything up again.
http://www.ebay.ca/itm/381034218782

(1) You begin by using a pocket knife to pop open the casings around both the USB A male and micro USB male connectors. Do this by firmly putting pressure via the blade edge on the seam between the casing halves. Once the blade has sunk about .5mm into the seam you then wiggle it to widen the gap. It may help to increase pressure on the seam by hinging the metal connector against the plastic (as if it was plugged in and someone decided to sit on the plastic). You'll see this when successful.


(2) Next, you take your soldering iron and move the green wire over to join the black wire, and the white wire over to join the red wire; on both connectors.
(3) Add a bit of a jumper between the D+ and D- connections on the micro USB connector (where the White and Green wires used to be) You'll see this when done.


(4) Finally, put the plastic connector covers back on and cleanly wrap them with some electrical tape.

I use Waze on my N5 every day during my commute to and from work. I find that the only micro USB cable I have that can still charge my N5 while running Waze is the OEM LG cable that came with it. I don't like the current state of affairs - where I'm reliant on just one cable with no backups.
WHAT
I've tried the regular 'Genuine' micro USB cables from China via Ebay that purport to handle Galaxy Note level charging, as well as 24/28 AWG cables that are supposed to handle increased currents. No joy.
NEED
- Pocket Knife
- Soldering iron + associated materials
- Electrical tape
HOW
I used a cheap, China, Ebay, micro USB cable that has a hard plastic casing around the connectors on either end of the cable; this makes it easier to pop the casing off, fiddle with the wires, and close everything up again.
http://www.ebay.ca/itm/381034218782
(1) You begin by using a pocket knife to pop open the casings around both the USB A male and micro USB male connectors. Do this by firmly putting pressure via the blade edge on the seam between the casing halves. Once the blade has sunk about .5mm into the seam you then wiggle it to widen the gap. It may help to increase pressure on the seam by hinging the metal connector against the plastic (as if it was plugged in and someone decided to sit on the plastic). You'll see this when successful.
(2) Next, you take your soldering iron and move the green wire over to join the black wire, and the white wire over to join the red wire; on both connectors.
(3) Add a bit of a jumper between the D+ and D- connections on the micro USB connector (where the White and Green wires used to be) You'll see this when done.
(4) Finally, put the plastic connector covers back on and cleanly wrap them with some electrical tape.
Jan 17, 2016
Pi Zero Project Box
Pi Zero Project Box:
Enclosure for a Raspberry Pi Zero information display (http://frederickvandenbosch.be/?p=1365)
Original enclosures: |
PiZero_InfoDisplay_front.stl |
ArdLock – Arduino Door Lock
ArdLock – Arduino Door Lock:
EswarD2 @ instructables.com has build an Arduino based door lock using Arduino UNO, a keypad and a servo motor.
The post ArdLock – Arduino Door Lock appeared first on Electronics-Lab.
EswarD2 @ instructables.com has build an Arduino based door lock using Arduino UNO, a keypad and a servo motor.
This a door lock built as fun project.It is quite easy to build and a fun way to learn and improve your knowledge of arduino.I tried to add a 16*2 display but there werent enough GPIO pins on arduino Uno.If You are interested in adding a display you would need an arduino Mega.ArdLock – Arduino Door Lock – [Link]
The post ArdLock – Arduino Door Lock appeared first on Electronics-Lab.
LPG Sensor Alarm
LPG Sensor Alarm:
sameer @ sgprojects.co.in has build a LPG gas detection circuit based on LM358:
The post LPG Sensor Alarm appeared first on Electronics-Lab.
sameer @ sgprojects.co.in has build a LPG gas detection circuit based on LM358:
LPG gas detection project’s main idea is to implement the security system for detecting leakage of liquid petroleum gas in closed environment. In this project gas leakage is identified by using MQ6 gas sensor. A simple circuit with an Op-Amp IC is powered by a step down transformer and finally the alarm produces on detecting gas.LPG Sensor Alarm – [Link]
The post LPG Sensor Alarm appeared first on Electronics-Lab.
Jan 16, 2016
Using a $2 DS3231 RTC & AT24C32 EEprom from eBay
Using a $2 DS3231 RTC & AT24C32 EEprom from eBay:

From the comments on our ‘Using DS1307 and DS3231 real-time clock modules with Arduino‘ post, Edward Mallon writes:
Via the comments.
From the comments on our ‘Using DS1307 and DS3231 real-time clock modules with Arduino‘ post, Edward Mallon writes:
I’ve been putting the $1 DS3231 boards through their paces for quite a while now…and they have been performing well.More details at Edward Mallon’s blog.
Via the comments.
Make your own open hardware guitar amplifier
Make your own open hardware guitar amplifier:
ElectroSmash just released an open hardware guitar amplifier called the 1Wamp. Designed as a small and portable 1 watt amplifier loaded with all the features of big amps, the project was fully developed using only open source tools—like KiCAD, a design suite to create schematics and layouts in any platform.files and schematics here: Make your own open hardware guitar amplifier
We published a detailed analysis of each part of the amplifier so that anyone can contribute to improving or modifying it, as well as, sharing their thoughts and work on the 1Wamp forum.
The amplifier features:
- Tone/Volume/Gain controls
- Speaker/Cabinet output
- Headphones output with attenuator switch
- Aux/mp3 input
- 9V battery clip
- 9V DC boss style power input jack
How to build 1Wamp in 5 steps
Here’s a summarized version from our full documentation.
Step 0
You will need a soldering iron, lead, and cutting pliers. You can get the PCB from ElectroSmash, or build your own at home using the native files or PCB layout transfers from the forum.
Photo by Ray Rodriguez, CC BY-SA 4.0
Steps 1, 2, 3, and 4
Soldering the components to the PCB is easy; just follow the Bill of Materials and solder the parts, beginning with the small ones. Then put the larger components in place.
Some tips:
- Pay attention to diodes polarity, there’s a line indicating the correct position.
- Be careful with the electrolytic caps polarity, the negative lead (the short one) has to be placed in the round hole. The positive hole is always square-shaped and it is marked with a “+” symbol.
- Be patient soldering the big components perpendicularly, because they tend to be slightly tilted.
Step 5
It’s time to check your work. Double-check your PCB with the model, component by component, before powering it up. Use this checklist:
The circuit board fits into several enclosures (like the Hammond 1590B and 1591C), and the plastic cover can also be used as lighting plate.
- Visual inspection of the PCB bottom, there is no short circuits or long uncut leads.
- The polarized components are placed correctly: diodes and electrolytic caps.
Inject Packets with an ESP8266
Inject Packets with an ESP8266:
[Kripthor] sent us a link to his blog where he writes the Hello World of low-level networking. Basically he’s constructing his own packet and sending it. By itself this isn’t a bad thing. You could use this power for all sorts of networks-diagnostic good. And so, despite the ominous name of his blog post “ESP8266 Jamming”, he’s not really doing anything that bad — he’s just creating many fake WiFi beacon frames and sending them out every so often.
Which can apparently do bad things to some vulnerable routers. Who knew? Want to test yours?
Naturally we wanted to see how he was doing it, and we opened up the Arduino code in GitHub. It turns out that Espressif has written a
It also turns out that the ESP8266 will enter monitor mode, where it listens to all WiFi traffic regardless of the MAC address that it’s directed toward. [Pulkin] seems to have done the work for us and posted the code in his GitHub. Now things get nasty. Combining promiscuous monitor mode with some carefully constructed management frames can end up with a classic WiFi deauth denial-of-service attack on a $2 piece of hardware.
We think it’s tremendously cool that the ESP8266 packs such power, and we beg you all to use it responsibly. The last thing we want to see is the world littered with WiFi-DOS throwies. And the last thing you’d want is a visit from the FCC.
[Kripthor] sent us a link to his blog where he writes the Hello World of low-level networking. Basically he’s constructing his own packet and sending it. By itself this isn’t a bad thing. You could use this power for all sorts of networks-diagnostic good. And so, despite the ominous name of his blog post “ESP8266 Jamming”, he’s not really doing anything that bad — he’s just creating many fake WiFi beacon frames and sending them out every so often.
Which can apparently do bad things to some vulnerable routers. Who knew? Want to test yours?
Naturally we wanted to see how he was doing it, and we opened up the Arduino code in GitHub. It turns out that Espressif has written a
wifi_send_pkt_freedom()
function that just sends out whatever packet you’d like to the network. That was easy.It also turns out that the ESP8266 will enter monitor mode, where it listens to all WiFi traffic regardless of the MAC address that it’s directed toward. [Pulkin] seems to have done the work for us and posted the code in his GitHub. Now things get nasty. Combining promiscuous monitor mode with some carefully constructed management frames can end up with a classic WiFi deauth denial-of-service attack on a $2 piece of hardware.
We think it’s tremendously cool that the ESP8266 packs such power, and we beg you all to use it responsibly. The last thing we want to see is the world littered with WiFi-DOS throwies. And the last thing you’d want is a visit from the FCC.
Raspberry Pi Wind Measurement
Raspberry Pi Wind Measurement:
A well organized approach to a project is a delight to see. [Pavel Gesyuk] takes just that approach with the experiments on his blog. Experiment 13 is a multi-part series using a Raspberry Pi as the heart of a weather station. [Pavel] is looking at wind speed and direction, and temperature measurement, plus solar power for the station. One of his videos, there are many, is after the break.
The anemometer and direction sensors are stock units wired to a Raspberry Pi A+ using an analog to digital daughter board. The data from the temperature sensor is acquired using I2C. During one part of the experiment he uses an EDIMAX WiFi adapter for collecting the data.
Python is [Pavel’s’ language of choice for development and freely shares his code for others to see. The code collects the data and displays it on a monitor connected to the Pi. The experiment also attempts to use solar power to charge batteries so the station is not dependent on mains power.
The mechanical assembly shows attention to detail commensurate with his project presentation and we respect how well organized the work is.
Filed under: Raspberry Pi, software hacks, solar hacks

A well organized approach to a project is a delight to see. [Pavel Gesyuk] takes just that approach with the experiments on his blog. Experiment 13 is a multi-part series using a Raspberry Pi as the heart of a weather station. [Pavel] is looking at wind speed and direction, and temperature measurement, plus solar power for the station. One of his videos, there are many, is after the break.
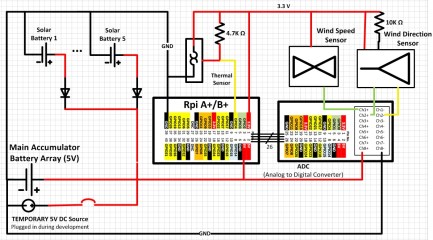
Python is [Pavel’s’ language of choice for development and freely shares his code for others to see. The code collects the data and displays it on a monitor connected to the Pi. The experiment also attempts to use solar power to charge batteries so the station is not dependent on mains power.
The mechanical assembly shows attention to detail commensurate with his project presentation and we respect how well organized the work is.
Filed under: Raspberry Pi, software hacks, solar hacks
Original enclosures: |
feature.jpg?w=150 |
ad516503a11cd5ca435acc9bb6523536?s=96 |
electrical_02_t.jpg |
Jan 14, 2016
Arduino 5 Minute Tutorials – Lesson 9 – Programming Arduino Platforms Using a Different IDE
Arduino 5 Minute Tutorials – Lesson 9 – Programming Arduino Platforms Using a Different IDE:

Lessons Menu:
- Lesson 1 – Software Downloading / Installing & Interface
- Lesson 2 – Basic Code
- Lesson 3 – Sensors: Potentiometers
- Lesson 4 – Sensor: Infrared Distance
- Lesson 5 – Actuator: Servo Motor
- Lesson 6 – Sensor: Force, Bend, Stretch
- Lesson 7 – Sensor: Accelerometer, Gyro, IMU
- Lesson 8 – Shield: Wheatstone Bridge & LCD
- Lesson 9 – Programming Arduino Platforms Using a Different IDE
So, you’ve installed the Arduino IDE and used it for a little while but now you are looking for something different. Maybe it wasn’t quite what you expected, it is too complicated, simple or something else that doesn’t meet your requirements. Well, there is hope! In this article we present to you other software options for programming your Arduino platform with. In this list of alternatives, we decided to split them into two major categories: visual programming and regular programming. Since this is only a short list of possible tools to program your favorite Arduino platform with, please let us know in the comments what you use (and why!) or any other thoughts on the options proposed here or others that we haven’t listed. |
Visual Programming
These alternatives provide the user with the ability to create programs graphically instead of writing code (text).Regular Programming
These allow you to code as normal (text), but provide a different interface and features to help improve your experience by facilitating some advanced tasks usually not possible with the Arduino IDE.ArduBlockWhile this one has not been updated in a little while, it is still a nice interface and can help you learn Arduino programming using blocks. You can download from sourceforge directly here. The main website seems to be down recently but you can see the Getting Started guide using a backup from archive.org for now. |
|
BlocklyDuinoThis is a web-based visual programming editor. It is based on Blockly.You can see a demo here and get the source code here to install it locally. |
|
miniBloqLike ArduBlock, this software allows for visual programming Arduino platforms using blocks. You can download it here. We recommend that you also read the documentation. |
|
Modkit MicroAnother block based programming interface with slight differences. This one can both run locally or through a web browser.You can download it here or access it online directly here. |
|
Scratch for Arduino (S4A)S4A is a Scratch modification that allows for simple programming of the Arduino platform.You can find the steps to download & install it here. This one also offers Android communication. |
|
Atmel StudioAtmel is the manufacturer of the AVR chips used in making most Arduino (and Arduino-compatible) microcontroller boards. If you wish to create more complex projects, this software can certainly help with debugging and many other features. With recent versions, it also allows “one-click import” of Arduino projects. You can learn more about it here. |
|
CodeBenderThis option offers a web-based IDE where all your software is stored on the cloud. It also allows users to easily share software and collaborate with each other. You can check it out here. There is also an interactive demo showing the basics. |
|
EclipseEclipse is a well-known, open source and full-featured development environment that can be set up to work with AVR and Arduino by using a plug-in and some extra configuration. You can learn more about how to install it on the Arduino Playground. |
Subscribe to:
Posts (Atom)